Viện năng lượng mặt trời của Pháp INES đã phát triển các mô-đun tấm pin năng lượng mặt trời mới bằng nhựa nhiệt dẻo và sợi tự nhiên có nguồn gốc ở Châu Âu, chẳng hạn như lanh và bazan. Các nhà khoa học đặt mục tiêu giảm tác động đến môi trường và trọng lượng của các tấm pin năng lượng mặt trời, đồng thời cải thiện khả năng tái chế.
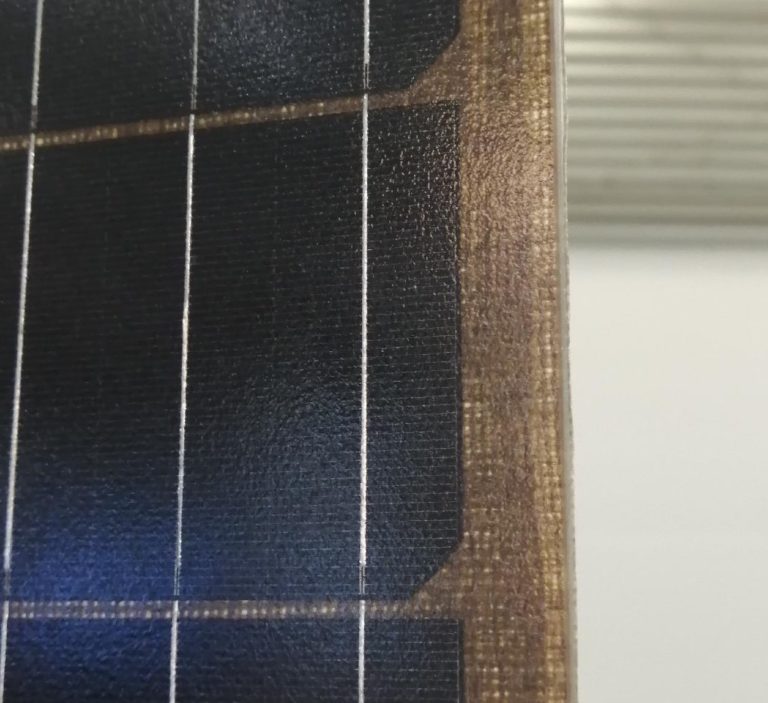
Một tấm kính tái chế ở mặt trước và một tấm vải lanh ở mặt sau
Hình ảnh: GD
Hình ảnh: GD
Các nhà nghiên cứu tại Viện Năng lượng Mặt trời Quốc gia của Pháp (INES) - một bộ phận của Ủy ban Năng lượng Nguyên tử và Năng lượng Thay thế Pháp (CEA) - đang phát triển các mô-đun năng lượng mặt trời có các vật liệu sinh học mới ở phía trước và phía sau.
Anis Fouini, giám đốc CEA-INES, trong một cuộc phỏng vấn với pv magazine Pháp cho biết: "Vì lượng khí thải carbon và phân tích vòng đời đã trở thành tiêu chí thiết yếu trong việc lựa chọn tấm pin quang điện, nên việc tìm nguồn cung ứng vật liệu sẽ trở thành một yếu tố quan trọng ở châu Âu trong vài năm tới."
Aude Derrier, điều phối viên của dự án nghiên cứu, cho biết các đồng nghiệp của cô đã xem xét các loại vật liệu khác nhau đã tồn tại, để tìm ra một loại vật liệu có thể cho phép các nhà sản xuất mô-đun sản xuất tấm nền cải thiện hiệu suất, độ bền và chi phí, đồng thời giảm tác động đến môi trường. Nguyên mẫu đầu tiên bao gồm các tế bào năng lượng mặt trời dị liên kết (HTJ) được tích hợp vào một vật liệu tổng hợp.
Derrier cho biết: “Mặt trước được làm bằng polymer chứa đầy sợi thủy tinh, mang lại độ trong suốt. Mặt sau được làm bằng composite dựa trên nhựa nhiệt dẻo, trong đó dệt hai loại sợi, lanh và bazan, đã được tích hợp, sẽ cung cấp độ bền cơ học, nhưng cũng có khả năng chống ẩm tốt hơn.”
Cây lanh có nguồn gốc từ miền bắc nước Pháp, nơi toàn bộ hệ sinh thái công nghiệp đã hiện diện. Bazan có nguồn gốc ở những nơi khác ở Châu Âu và được dệt bởi một đối tác công nghiệp của INES. Điều này làm giảm lượng khí thải carbon 75 gam CO2 trên mỗi watt, so với một mô-đun tham chiếu có cùng công suất. Trọng lượng cũng được tối ưu hóa và nhẹ hơn 5 kg mỗi mét vuông.
Derrier nói: “Mô-đun này nhằm ứng dụng vào các tấm PV trên mái nhà và tích hợp tòa nhà. Ưu điểm là có màu đen tự nhiên, không cần tấm mặt lưng. Về mặt tái chế, nhờ nhựa nhiệt dẻo có thể nấu chảy lại nên việc tách các lớp về mặt kỹ thuật cũng đơn giản hơn ”.
Mô-đun có thể được làm mà không cần điều chỉnh các quy trình hiện tại. Derrier cho biết ý tưởng này là chuyển giao công nghệ cho các nhà sản xuất mà không cần đầu tư thêm.
Bà nói: “Điều bắt buộc duy nhất là phải có tủ đông để bảo quản vật liệu và không bắt đầu quá trình liên kết nhựa, nhưng hầu hết các nhà sản xuất ngày nay đều sử dụng prepreg và đã được trang bị cho việc này.”
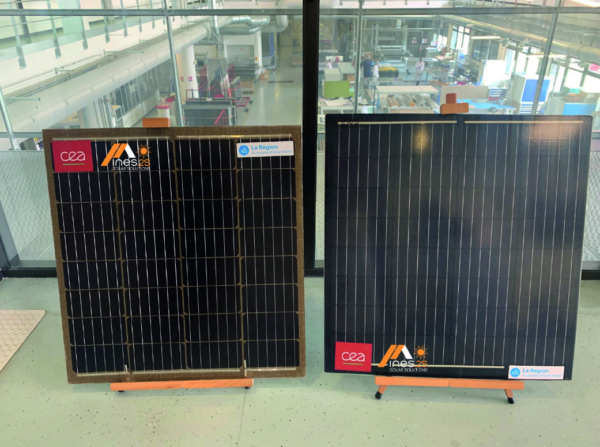
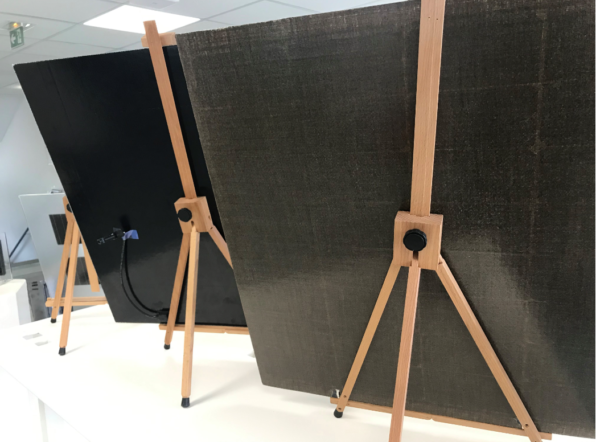
Các nhà khoa học của INES cũng xem xét các vấn đề cung cấp kính năng lượng mặt trời mà tất cả các nhà sản xuất quang điện gặp phải và nghiên cứu việc tái sử dụng kính cường lực.
Derrier cho biết: “Chúng tôi đã làm việc trên đời thứ hai của kính và phát triển một mô-đun được tạo thành từ thủy tinh 2,8 mm được tái sử dụng từ một mô-đun cũ. Chúng tôi cũng đã sử dụng chất bao bọc bằng nhựa nhiệt dẻo không yêu cầu liên kết chéo, do đó sẽ dễ dàng tái chế và một hỗn hợp nhựa nhiệt dẻo với sợi lanh để tăng khả năng chịu đựng.”
Mặt sau không có bazan của mô-đun có màu vải lanh tự nhiên, ví dụ, có thể thú vị về mặt thẩm mỹ đối với các kiến trúc sư về tích hợp lên mặt tiền công trình. Ngoài ra, công cụ tính toán INES cho thấy lượng khí thải carbon giảm 10%.
Jouini nói: “Bây giờ bắt buộc phải đặt câu hỏi về chuỗi cung ứng quang điện. Với sự giúp đỡ của vùng Rhône-Alpes trong khuôn khổ Kế hoạch Phát triển Quốc tế, do đó, chúng tôi đã tìm kiếm những người chơi ngoài lĩnh vực năng lượng mặt trời để tìm loại nhựa nhiệt dẻo mới và sợi mới. Chúng tôi cũng đã nghĩ về quy trình cán mỏng hiện nay, tốn rất nhiều năng lượng ”.
Giữa giai đoạn điều áp, ép và làm nguội, quá trình cán mỏng thường kéo dài từ 30 đến 35 phút, với nhiệt độ hoạt động khoảng 150° C đến 160° C.
Derrier cho biết: “Nhưng đối với các mô-đun ngày càng kết hợp các vật liệu được thiết kế sinh thái, cần phải biến đổi nhựa nhiệt dẻo ở khoảng 200° C đến 250° C, biết rằng công nghệ HTJ nhạy cảm với nhiệt và không được vượt quá 200° C”.
Viện nghiên cứu đang hợp tác với chuyên gia nén nhiệt cảm ứng Roctool có trụ sở tại Pháp, để giảm thời gian chu kỳ và tạo hình theo nhu cầu của khách hàng. Cùng nhau, họ đã phát triển một mô-đun có mặt sau được làm bằng composite nhựa nhiệt dẻo loại polypropylene, trong đó các sợi carbon tái chế đã được tích hợp. Mặt trước được làm bằng nhựa nhiệt dẻo và sợi thủy tinh.
Derrier cho biết: “Quy trình nén nhiệt cảm ứng của Roctool có thể làm nóng hai mặt phía trước và phía sau một cách nhanh chóng mà không cần phải đạt đến 200° C ở lõi của các tế bào HTJ”.
Công ty tuyên bố khoản đầu tư thấp hơn và quy trình có thể đạt được thời gian chu kỳ chỉ vài phút, đồng thời sử dụng ít năng lượng hơn. Công nghệ này nhằm vào các nhà sản xuất composite, nhằm mang lại cho họ khả năng sản xuất các bộ phận có hình dạng và kích thước khác nhau, đồng thời tích hợp các vật liệu nhẹ hơn và bền hơn.
Nguồn bài viết: pv magazine.